Carbon Fiber 101 1488
Carbon Fiber 101
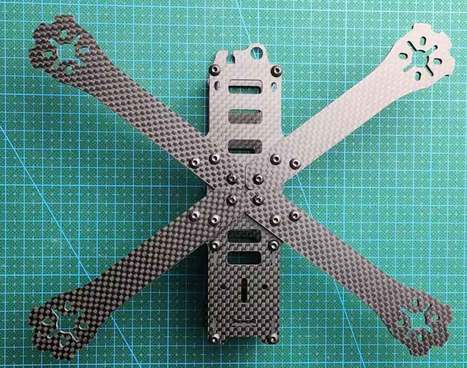
Jinjiuyi is a carbon fiber drone frame manufacturer in China, we offer best drone frames cutting service.
custom drone frame
Who out there has heard of carbon fiber? Do you even know what it is? It has become apparent to me over the past few months that almost everyone in the sport compact scene is aware of carbon fiber as it explodes in popularity. It is being used to manufacture everything from the popular hoods to even fenders and interior pieces now. But another thing that became apparent is that although many enthusiasts are aware of it, very few actually know what it is. Well in this month's column we will discuss where carbon fiber came from, the properties of the material, and how it is used.
Carbon fiber has been around for over fifty years with its earliest history in the aerospace and military industries. It was normally reserved to these industries as the costs of manufacturing carbon fiber were sky high, and cost consideration is low in these two industries. Only in recent years has production of carbon fiber climbed, therefore lowering the price and making its use more widespread.
best carbon fiber drone frame
Carbon fiber can be produced in one of two ways. These are "wet" lay-up and pre-impregnated lay-up processes. The "wet" process has been used since the beginning of composites. It creates molded shapes from glass or carbon fiber and resin. Do-it-yourselfers use this practice extensively as it is the least labor intensive and expensive money wise. When manufactured in the "wet" lay-up, dry fibers are laid into a mold and resin is poured onto them. The resin is then brushed over the fibers in a relatively uncontrolled manner. Resin is added in layers and layers until the desired thickness is achieved. If this process is not performed correctly the fibers can become saturated with resin which causes added weight, and reduced strength and stiffness. This method can also create inconsistent products as certain areas are saturated and others are not thick enough.
Pre-impregnated lay-up has been refined over the past 20 years to create better products with more predictable results. In this method the fibers are pre-impregnated with resin at the factory. It is then rolled onto spools and then frozen to prevent the material from curing too quickly. Materials made by this method are typically 20-30% stronger than "wet" laminate of the same thickness. Pre-impregnated lay-up materials can be cured in one of two ways: vacuum bag compaction and also vacuum bag compaction plus an auto clave. The composite is placed under vacuum bag compaction and is placed into an oven. The resin will then solidify or "glass." When the autoclave is used it essentially pressure cooks the fibers. The maximum allowable temperature of the cured laminate is used and the continuous temperature is lower. It is normally is between 250 and 350 degrees.
Automakers first began experimenting with carbon fiber in the 1970s. Ford even built an entire car out of carbon fiber composites in 1977. In the 1990s GM manufactured a concept car out of carbon fiber that got 100mpg. The motivation for automakers is to produce vehicles with lower emissions, lighter weight, lower cost and better fuel economy. The problem carbon fiber has presented though in the past is its astronomical price compared to other materials. At one point, it cost $100 per pound versus .40 cents for steel. Nowadays though, the prices are hovering somewhere in the $5-$10 price range and it is making many other industries experiment with the material. Many enthusiasts purchase carbon fiber products solely for the looks, but they offer other benefits as well. Carbon fiber reinforced materials perform at higher rates for strength versus steel and aluminum.